Home > Case studies > Using EMG sensors in an industrial environment
Using EMG sensors in an industrial environment
BACKGROUND
ALSTOM Transport (Reichshoffen site in Alsace, France) is using the CAPTIV system (sensors & software) developed by T.E.A., for a variety of research purposes. An example is the evaluation of the tightening activity, with the aim of defining ergonomics criteria and designing a
matrix of selection for tightening tools. The tigntening activity is prominent indeed in the production facilities of ALSTOM Transport. This activity is currently very demanding on upper limbs.
A user test was conducted on twenty operators in order to obtain representative and objective data with the following equipment:
- A tightening test bench,
- 5 Electromyography (EMG) sensors (for measuring electrical activity on muscles),
- A camcorder
- The CAPTIV software.
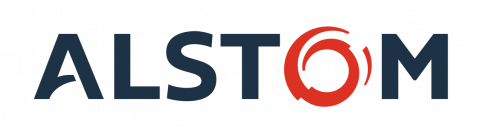
« CAPTIV by T.E.A. is a truly innovative way to measure the ergonomics of our current and future activities at Alstom, by capturing reliable and accurate data. »
THE MEASUREMENTS
Two types of tools were tested on the tightening bench: torque wrenches (with various settings) together with electric and offset screwdrivers (with various torque settings and rotation speeds). Five EMG sensors were positioned on five separate muscles (figure 1) on the subjects. The selected muscles (brachioradialis, biceps, triceps, pectoral and deltoid) are the most representative and used during the tightening activity. Each sensor was assigned to a muscle via its serial number. Following the defined protocol, the operators needed to perform various tightening operations in various positions on the bench (figure 2).
Figure 1: Position of EMG sensors on the operator
Figure 2: Various tightening positions tested
The CAPTIV system was used for recording in real-time the sensors’ measurements together with synchronous video. Coupling measurement with images allowed for a more detailed analysis of the muscle strength deployed by the subjects during the tightening activity (figure 3).
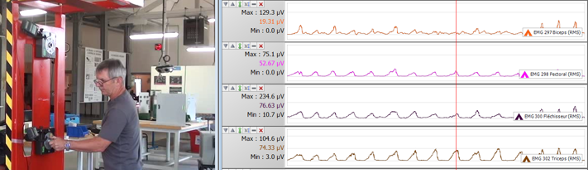
Figure 3 : EMG sensors data coupled with video
Conclusion
EMG sensors enable to measure the electrical activity of a muscle which can be converted in muscle strength in a variety of application scenarios. Their main advantage is that they are sufficiently robust for allowing repetitive trials in the field with multiple operators. This enabled to collect representative and objective data in real situations by measuring the muscle strength of the operators in each position on the test bench. The EMG data also enabled to compare the genuine muscle strength with the % Maximum Voluntary Contraction (MVC) threshold that should not be exceeded, and therefore to determine the maximum torques and the maximum tightening frequencies. Therefore, this study enabled to target the most ergonomically suited tools for each work situation, while preserving the operators’ health.